
Our Process
Innovation

Pot Still Process
• After distillation is complete, the whole stillage is transferred to the stillage collection tank as quickly as possible to allow for a follow on distillation run.
• From the stillage collection tank, the whole stillage is pumped to the rotary drum screen (RDS) at a fixed rate. The rate needed/required will determine the size of the equipment that will be installed. The RDS thickens the whole stillage before it enters the screw press.
​
• The filtered thin stillage from the RDS is either collected to be used as backset or discharged. Filtering the stillage through the RDS has the potential to reduce the organic load by 60% and the solids loading by 98%. This is a significant reduction in discharged waste and positive environmental impact.
• When used as backset, it allows for higher inclusion rates without increasing viscosity.
• The screw press removes all the unbound water from the ddgs producing a 40% dry ddgs that will flow like a dry grain simplifying transport or disposal. Farmers are more inclined to want to pick up dry ddgs than whole stillage.
Column Still Process
• The beer feed rate to the column dictates the size of the stillage equipment. The beer bottoms pump runs continuously at varying rates to maintain the level in the bottom of the column.
• The whole stillage enters the rotary drum screen (RDS) at 8 - 9% solids. The drum screen filters the thin stillage and thickens it to 16-18% solids.
​
• The thin stillage is now 98% reduced in solids and can be treated to reduce the organic load by up to 60%. The thin stillage can be recycled as very clean backset or discharged with a significant reduction in environmental loading.
​
• The stillage solids then drop into the screw press where the remaining liquid is pressed off the grain. The ddgs exit the screw press at 38 - 40% dry solids. The ddgs will look and act like dry grain.
​
• The screw press removes all the unbound water from the ddgs producing a 40% dry ddgs that will flow like a dry grain simplifying transport or disposal. Farmers are more inclined to want to pick up dry ddgs than whole stillage.
• Implementing the SOS system enables increased production capacity of the plant by reducing the frequency of spent stillage disposal and increasing daily production.
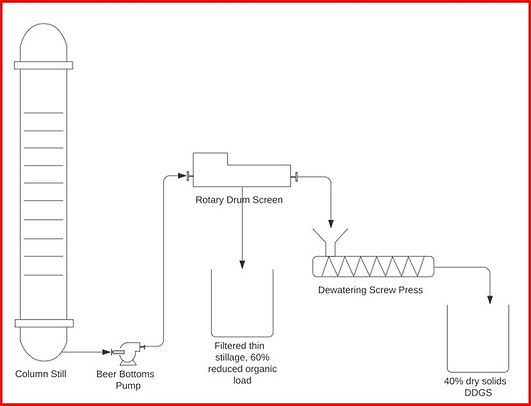


Rotary Drum Screen
• The rotating drum screen (RDS) is necessary as a pre thickening step ahead of the screw press. Pre-thickening increases the throughput capacity of the screw press while simultaneously producing high quality thin stillage or backset. Without the RDS the screw press is unable keep up with even a small flow of whole stillage.
• The RDS is specifically designed to deal with the challenges of hot acidic stillage and is capable of continuous 24/7 operations.
​
• The gear box and drive system are reliably designed to reduce vibrational load on the gear box to extend system longevity. The drive system allows for higher RPM than other RDS machines. The higher RPM's greatly increases capacity for similar size units.
​
• The screen and RDS casing are all stainless steel and the systems can be made to be vapor tight.
​
• The RDS's can be made in any size or combination to meet the needs of any distillery.
​
• SOS has operational systems that handle ranges of 8 gpm to 150 gpm of stillage.
Screw Press
• To achieve 40% dry ddgs, pressure is be applied to the ddgs. The screw press uses a pneumatic cone at the end of the screen/draining section to create pressure. The auger continues compressing the ddgs against the outlet cone forcing the remaining unbound water off the ddgs.
​
• Screw presses lack the ability to remove large volumes of free water. Therefore, if whole stillage is supplied to a screw press the throughput capacity (gallons/hour) of the press drops exponentially when compared to stillage that has been pre-thickened by the SOS RDS.
​
• The use of the screw press is not a requirement in the process. Using the screw press simplifies disposal of the ddgs.
​
• Farmers prefer dryer ddgs for ease of transportation (less water) and they are easier to store and use as feed on the farm.
​
• Installing the screw press is really about improving the format of ddgs that are available to the farmer.

CONTACT
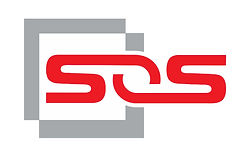